Project Date: 2019-2020
Project Roles: Lead Mechanical Designer
Project Abstract:
To modify an existing Traxxas X01 with various sensors and mechanical upgrades to allow full autonomous control. The project is to be presented at AIM Boston 2020 student design competition and be used in a doctorate students PHD dissertation.
Project Description:
To create an autonomous RC car, it is important to have as many sensor inputs as possible to allow as many variables be used in the control loop. The team consisted of four members – a lead mechanical designer, lead controls programmer, and programming assistant. As the only one on the team with some sensor knowledge and mechanical design knowledge, it was my job as lead mechanical designer to do all mechanical retrofits of sensors and design upgrades to the car.
The first order of business was to determine what sensors needed to be retrofitted. The school has already purchased a Traxxas X01 RC car before I joined the project. This itself poised some challenges, as a commercial RC car was not meant to have mounting for any sensors that we needed. If we were to do this again, a custom designed platform would be created. Sensors that needed to be added where:
– Wheel speed sensors
– Steering sensor
– Nvidia Jetson Tx2 control board
– Accompying electornic hardware
– LED tracking Lights
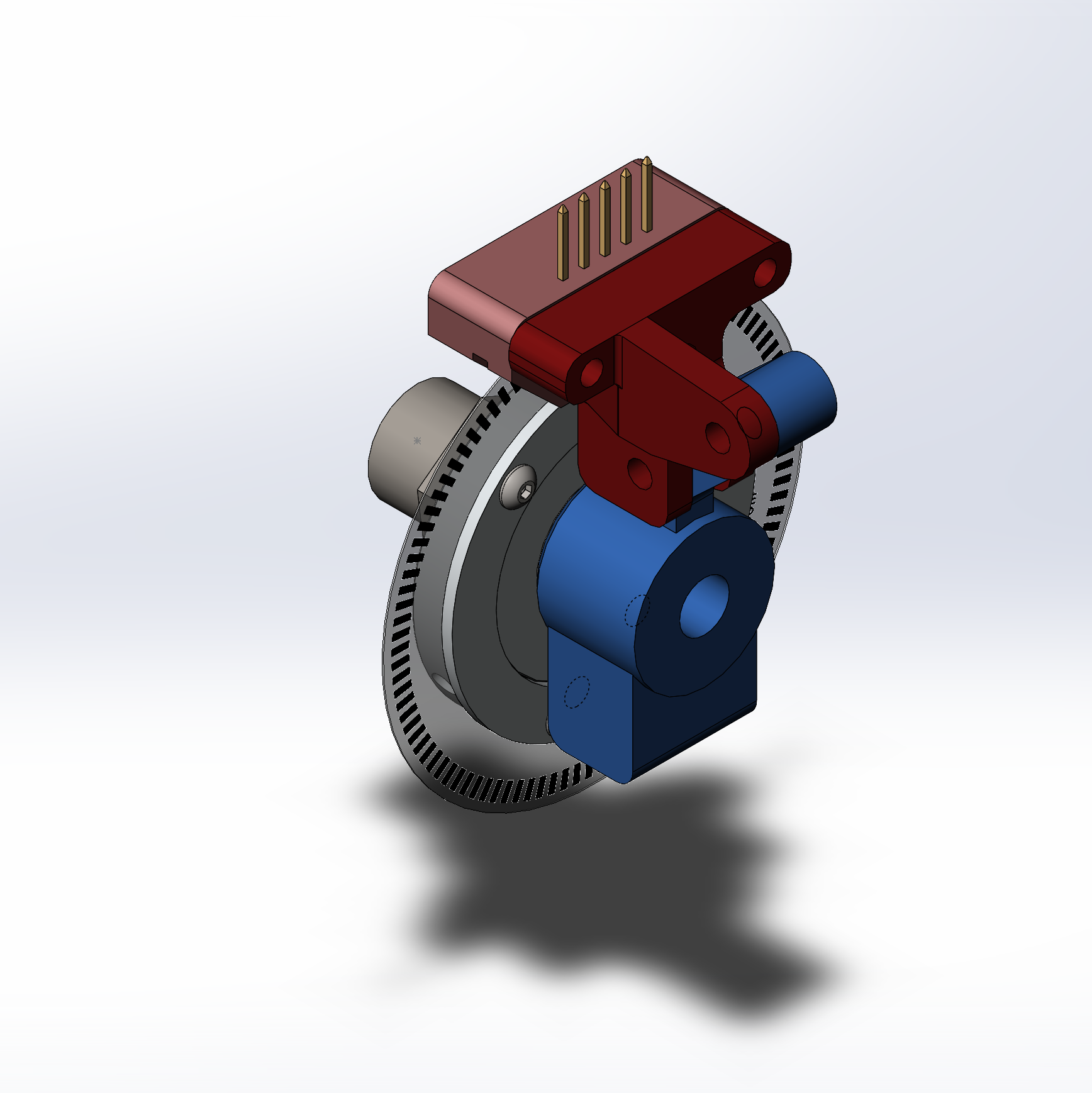
Wheel speed sensors needed to be attached directly to each wheel, and unfortunately there were no simple mounting holes on the wheel uprights. The uprights were measured and re-modeled in CAD, where mounting holes used for linkages were used to create a 3D printed mounting bracket and spacers where the optical encoder disk and sensor would be placed. The optical encoder disks we purchased did not fit over the cars existing axles, so custom axles and disk holders had to be machined. Photos in the gallery bellow show some of the parts modified and created.
As the lead mechanical designer, it was very important that I was included in all discussion about sensor selection and the designs I have developed were strong enough to handle persistent testing. There was a constant stream of communication between the controls and me, as sensors needed to fit packaging wise while conforming to the requirements they need. When creating longer axles and mounting for electronics, it was important that weight is distributed evenly to not upset the handling characteristics and geometry not change about a certain threshold. Unreliable designs that broke or needed frequent tweaks would mean more downtime in testing.
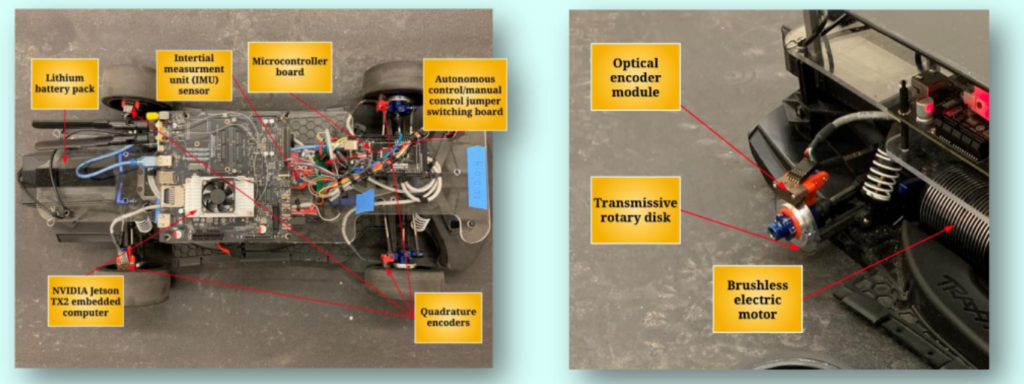
After the the parts were added to the Traxxas X01, another projected was started by another graduate student using a similar Traxxas truck platform. Sharing a lot of parts, similar wheel encoders and steering sensors were easily added.
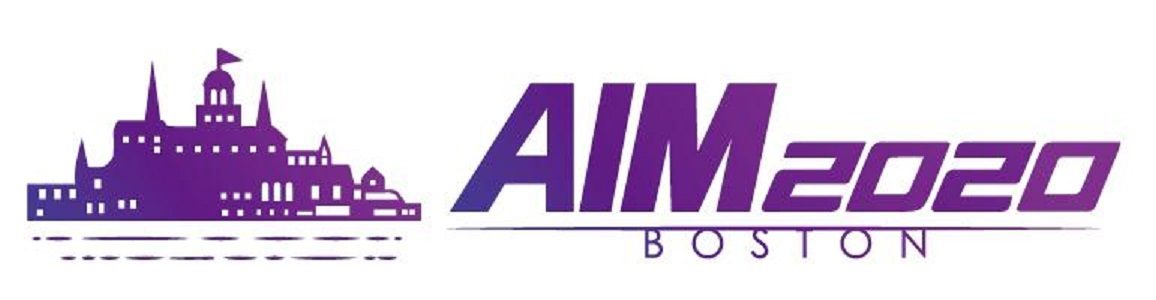
In 2020, me and the other undergraduate student responsible for programming the RC car presented at the Boston AIM 2020 student design contest, where universities all across the world presented their designs and innovations in the realm of automation and mechatronics. Due to our project advisor also being an event organizer, we were not eligible for the main competition or main prizes. However, our presentation and work on the project still vetted us a honorable mention, putting us up with universities from China and the EU. Below in the gallery was our project poster and reward certificate.
Personal Learnings From This Project
By this time, most of the designs I have worked on were on a larger scale. I was also on the Rutgers Formula Racing Team on this time as well, so my knowledge on larger automotive engineering translated extremely well to even the smallest of scales. The importance of 3d printed parts must not be understated here as it allowed for extremely intricate designs to time consuming to be made by a CNC machine. Alongside mechanical design, I have always personally believed that any mechanical engineer in this current era should be extremely good at programming and controls. This project helped me get a glimpse on the deeper side of autonomous control of vehicles and most importantly, relating the handling to actual car characteristics. Even on the small scale, the same physics apply and dynamics on a larger vehicle translate really easily, as it is only a matter of larger scale.
I would like to thank Alborz Jelvani, Kuo Chen, Jaixing Yu, Jingang Yi, and Ali Arab for helping on this project and having the pleasure to work alongside with them.
Project Photos and Project Poster/Award:
All parts shown were designed by me with various manufacturing methods.