Project Date: 2018-2021
Project Roles/Leadership: Lead Machinist, Controls Design Lead
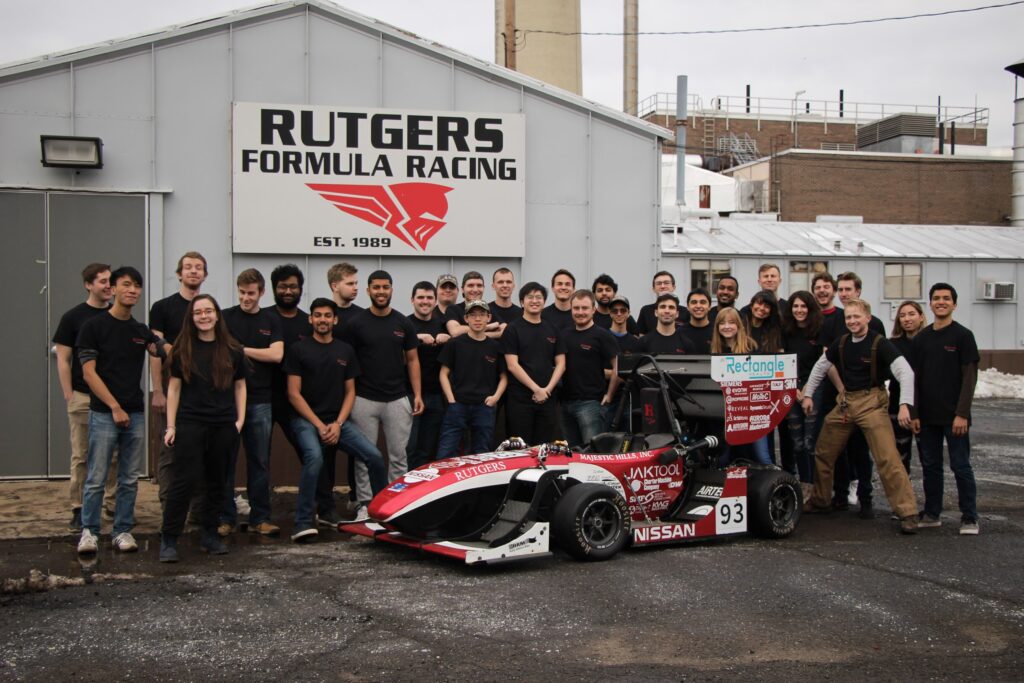
Project Abstract:
To design, test, and compete a competition ready car in the student Formula SAE (FSAE) competition
About the Project:
Back when I took a tour of the Rutgers University Engineering clubs, I was introduced to the Rutgers Formula Racing team (RFR). I was instantly hooked as I am an extreme gearhead and have an extreme passion for automotive engineering. If I am being completely honest, RFR was the main reason why I decided to go to Rutgers for engineering. In 2018, when I was in my freshman year, I joined the club. Eager to learn and become an important member on the team, I attended all the meetings, did all the trainings and became a member within the first month of joining. Wanting to make myself useful and learn new skills, I took up learning how to machine (By the time new member signups were around, that years car was already designed). Having been previously exposed to additive manufacturing (Custom built 3D printer) I was aware of the basic principles of machining. When I actually got on the manual mill, I was able to get a handle of things relatively quickly. Before I knew it, I was machining some basic critical components for the team, such as chassis welding jigs, brake disc hardware, and other various components.
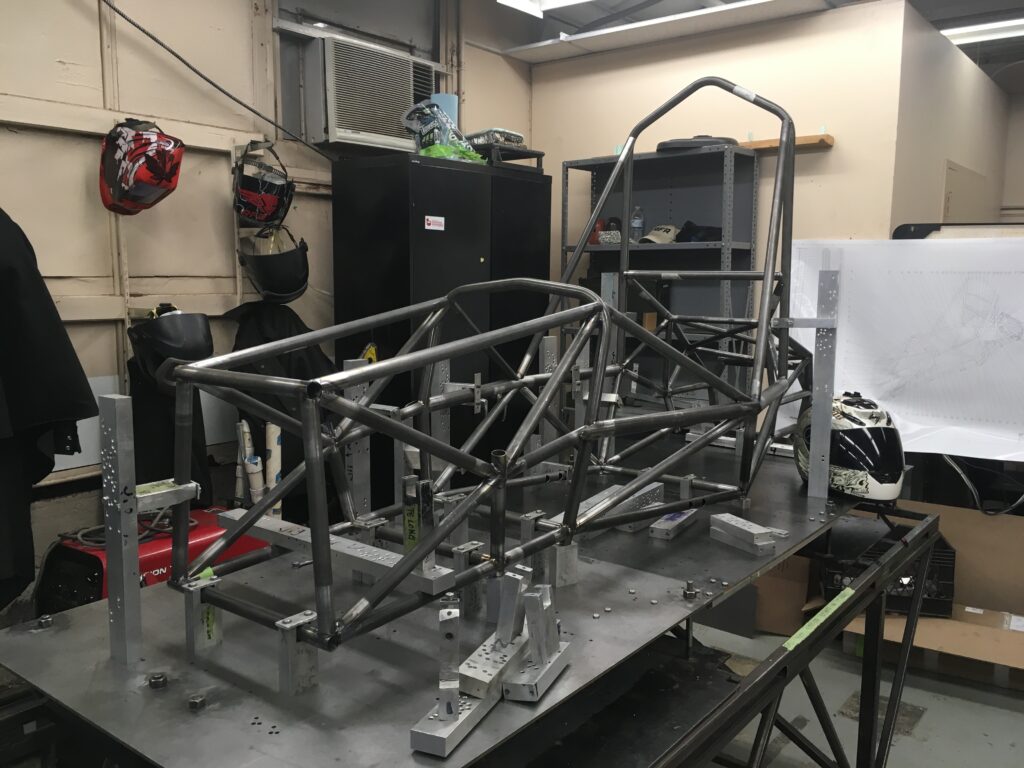
However, I was always particularly interested in learning how to use the CNC machine the team had. On the team, CNC machining was not a skill the majority of the team knew how to do. In fact, only three members at that time were competent enough to reliably machine parts to be put on the car. I was eager to learn, and was mentored by a senior on how to program the CNC. I also caught on really quickly, and before I knew it, I was CNC’ing critical components for the car including fuel injector bungs, differential carriers, suspension rockers, and controls hardware.
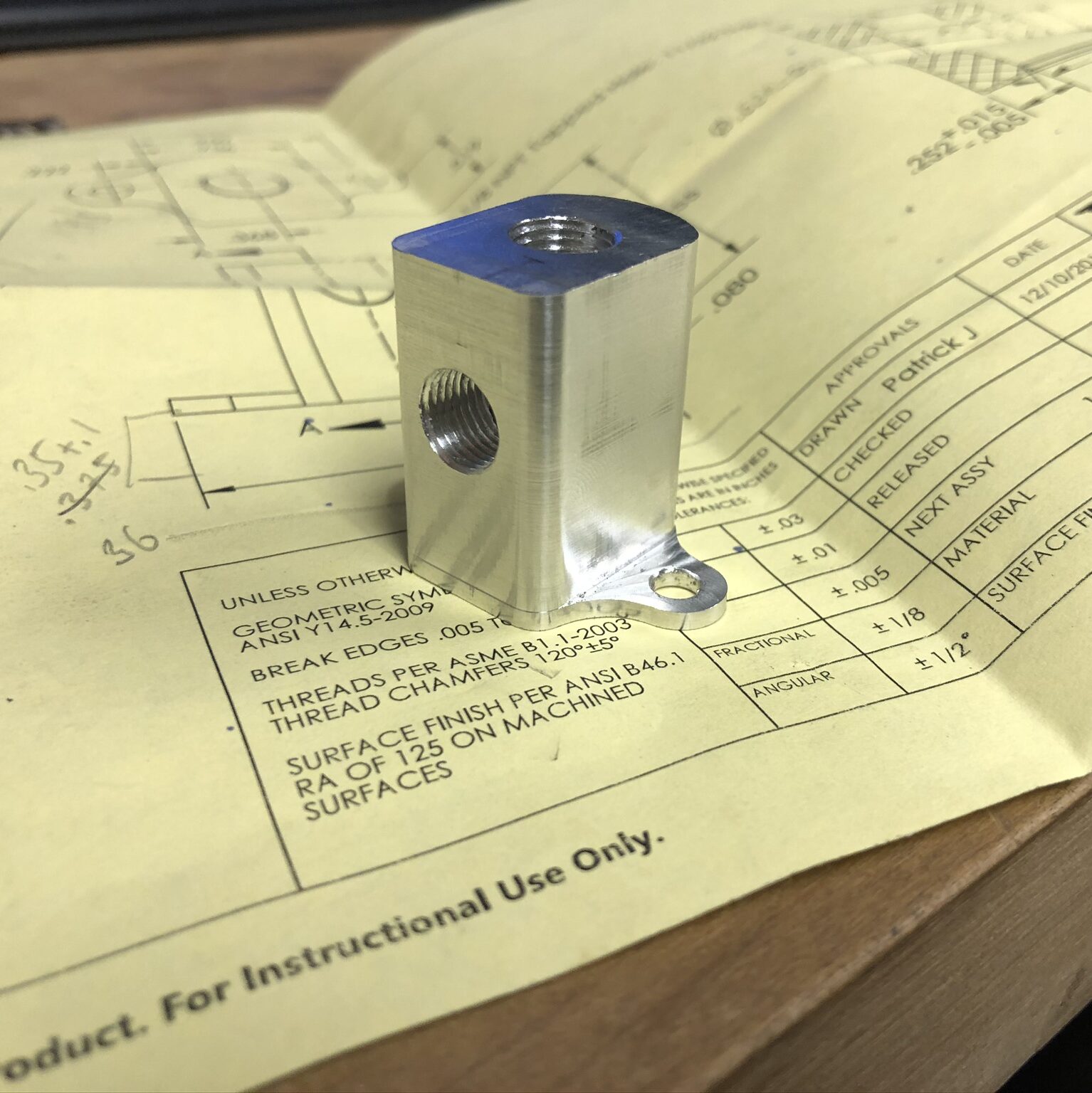
My ability in manufacturing did not go unnoticed, and I was asked to be the first ever Lead Machinist (Surprisingly, the team did not have an official “Lead Machinist” before me). It was my responsibility to ensure the machine shop was a safe and clean workspace, and that all the machines were in working condition. I retrofitted some machines with modern digital read out equipment, and I created a learning plan to teach new members how to machine safely and effectively. Every new member on the team had to go through me and my training plan to be certified on machine shop safety and how to use the machines. During the manufacturing season, I was responsible for creating a realistic manufacturing plan with estimating how much time certain parts would take to machine and distributing the work amongst the members. The experience I earned from machining laid a solid foundation for strong mechanical design, as understanding how a part is made also correlates to parts that can actually be made and assembled. After my time as lead machinist, I took up the role as controls design lead. Alongside my team leader duties, I took responsibility for re-designing the pedal box, and shifter mechanism – both overlooked parts of the car.
My duties as controls lead were general design direction and designing some parts. The subteam in general was a small one, so I was in charge of four other students designing parts. In the team lead meetings, it was my responsibility to rely the tasks of the week and information down to my subteam. Within the subteam, I was in charge of the general direction of part design and went over designs with the members whenever they completed a revision. I was able to expand my leadership skills and practice leadership in an engineering setting.
There wasn’t ever an official design for the shifter mechanism on previous years car, as time was running out and a temporary part was made (They say, there is nothing more permanent than a temporary solution). The “temporary” part was difficult to machine, and flexed tremendously under the pneumatic shifters operation. This lead to concerns over long term reliability and design judges were not to happy with the lackluster design. I sought to rectify this by simplifying the design to be made easier with the CNC, and run proper FEA analysis to ensure the part is strong enough to handle the rigors of competition, and to be documented for design judging. The pneumatic cylinder used for shifting was enlarged to be able to run lower pressures and ensure enough force was available to shift the gearbox (The motor/transmission was a KTM engine used on a dirt bike) The end result was a surprisingly simple shifter mechanism and a part that was overall ~30% lighter than the previous part, but magnitudes stiffer.

The pedal box was a design that remined unchanged within the team for many years. The design was proven and reliable, but changing position of the pedals was cumbersome and took several minutes to undue all the fasteners and move the pedals. This was reflected poorly by the judging score reports and this was another issue I sought to rectify. Taking inspiration from the LaFerrari’s moveable pedal box (The supercar did not have adjustable seats, leaving the pedals to be the only point of adjustment for different driver heights, similar to our FSAE car) I created a sliding pedal box that is locked with ball indent pins. FSAE rules require critical hardware be constrained by positive locking hardware, and these ball indent pins with buttons were legal. This meant changing pedal position was a matter of sliding four pins out and sliding the pedals. This brought adjustment time down to mere seconds.
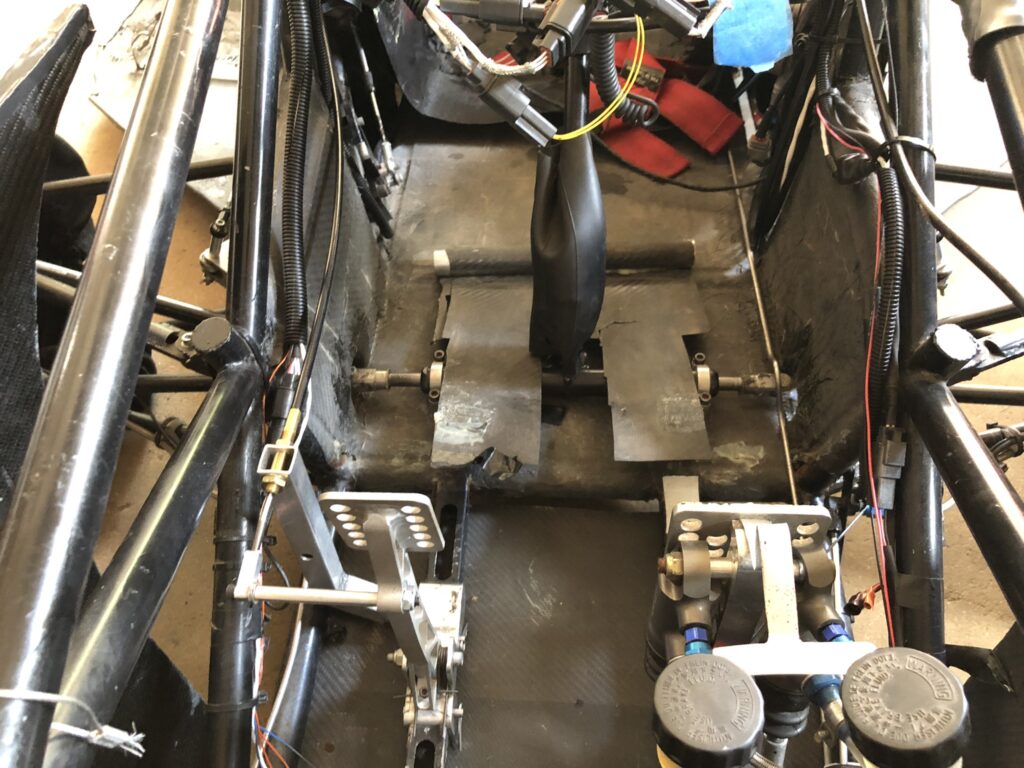
When the pandemic hit in 2019, the FSAE competition went virtual, and that year we refined further designs and presented a virtual design to the judges that year. I retained my position as Controls Lead and created a design to experiment with gas-shock rebound springs for the pedals, with the promise of smoother pedal feel. This was primarily done as other teams ran similar setups, but was never tested.
Project Photos:
Pedal Box View Accelerator Pedal Injector assembly all together Injector bung fresh off the cnc Injector bung fresh off the cnc Differential carrier Shifter assembly Shifter assembly Shifter assembly part Hole taper for injector Injector bung fresh off the cnc Backup driver Front rocker arms Rear rocker arms Upright fixtures Upright fixtures Upright fixtures Upright fixtures Floating brake assembly Rocker arms installed Rocker arms installed Shifter assembly part Custom standoffs Suspension Arm fixture Tube chassis being welded